|
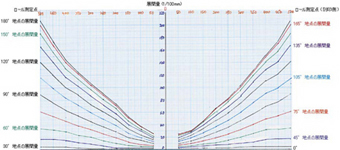
Click to enlarge |
|
At this time, I'd like to ask you about your Flat Expander (FE) rubber-cord-type wrinkle removing roll. First, on what principle can a web be expanded with a no-bow, straight roll? |
Tsuchida: |
When the loci of several points on a bow roll being rotated are traced, it is found that they spread, essentially in a loose V shape, at incremental angles from the roll center outwards toward the roll ends. Such expansion loci are incorporated in a straight roll. |
|
Can you explain more fully? |
Tsuchida: |
Provisions are made so that the both outer end members of a straight roll can be rotated as inclined, and so that a number of rubber cords installed between these end members in the roll's longitudinal direction are repeatedly expanded and contracted. Such an arrangement can basically realize the expansion loci of a bow roll with a no-bow, straight roll. Our Flat Expander is abbreviated as FE. Now, I will explain the FEÍs expansion principle referring to the following illustration.
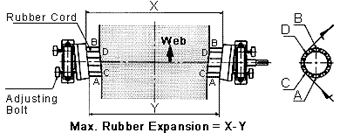
Two adjustable bolts are attached to each of the FE's outer end members. When the adjustable bolts at the web inlet side A are fastened and the adjustable bolts at the web outlet side B are loosened, the both outer end members are inclined. In a side elevation, the FE's roll body is made in the shape of a trapezoid in which the upper side is longer than the lower side. During the rotation of the roll body, each rubber cord undergoes maximum contraction at point A and then maximum expansion at point B. Accordingly, a web wound on the roll body at a point C (the rubber contraction point) is expanded at a point D (the rubber expansion point). This expands and spreads the web, resulting in natural wrinkle or crease removal.
|
|
In other words, when a point P on a rubber cord is moved to a point P' with the rotation of the roll, the point P' is located outward with respect to the original point P. That is, the rubber cord is stretched outwardly, and the web wound on the rubber cord is spread outwardly, right? Well, why are rubber cords used, but not a rubber tube or sleeve? |
Tsuchida: |
In the beginning, I planned to make a straight expander roll with a rubber tube or sleeve. However, I found that while the structure for wholly stretching a rubber tube in its longitudinal direction can theoretically be done, there were a number of problems in embodying such a plan. So I then started with rubber cords to be installed between the end members, which can be rotated while inclined. At any rate, unless a straight rubber member is uniformly stretched in its entirety, a web cannot be uniformly expanded throughout its width.
What I pondered then, was how could the rubber expansion curve be brought closer to an ideal one; for example, how could the expansion curve from the roll center toward both roll ends be made in as much of a linear and symmetric loose V pattern as possible. I am fond of birds. I often watch ducks, herons, gulls or other birds at the waterside. The moment they quickly fly into the air from the waterside, they spread the wings in a loose V shape. That beautiful loose V shaped wingspread was imprinted on my mind at the time. I made a sample FE, measured its expansion amounts, plotted them on a graph, and compared the resulting expansion curves with the wingspread of a bird. Then, I made an improved sample FE, measured its expansion amounts, and so on. I repeated these procedures until I got a minimally satisfactory FE roll.
It was long afterwards, about 15 years ago, that I developed the rubber-tube-type straight expander roll MIRAVO. We can talk about the MIRAVO roll later.
|
|
Then, did you finally get an ideal loose V-shape expansion curve close to a bird's wingspread? |
Tsuchida: |
Improvements in our FEs are still being made in order to get the expansion curve much closer to ideal. FEs have been continuously improved and developed over the years through the first generation, initially intended for textile products, the second generation developed for paper and plastic films, the third generation geared specifically toward higher-speed applications, and the fourth generation designed to respond to current high-end products in a variety of industries. Throughout these improvements and developments, the theme of "finding an ideal expansion curve" has always sounded as continuo. |
|
I always have the feeling of "only with a roll", But was it a succession of development over 30 years, wasn't it? |
Tsuchida: |
As I told you previously, I started developing a no-bow expander roll in response to a request for something which can expansively convey, among processing steps, a web in an unaffected, flat and intact manner without any excessive stretching, side-movement, slack, or wrinkling. However, the types of webs being processed have gradually increased from fabrics to paper, plastic films, nonwovens, glassfibers, metallic foils and so on, while the types of machines used have also expanded, from initial carrying machines and winders to weaving machines, driers, wrapping machines, coaters, laminators, printing machines, slitters, vacuum evaporators and so on. On the other hand, over these 30 years, Japan's manufacturing industry has worked together in pursuit of quality improvement, rationalization and cost cutting. So, it is a matter of course that I was thrown into a sea of technical innovations before I was aware. |
|
Now, your current FE rolls are fourth generation. Are the basic principles of spreading and expansion the same? |
Tsuchida: |
Yes. The basic principle hasn't changed. However, as webs have rapidly become thinner, wider, and faster, there have been some cases where uniform expansion cannot always be obtained with first and second generation FE rolls. So, they have continuously been improved in design, material, structure, and so on through the third and fourth generations. The thinner, wider and faster conditions to be met are factors that prevent ideal uniform expansion. So, I have made improvements to obtain, even under such conditions, an ideal loose V-shape expansion curve close to the wingspread of a bird |
|
And now, can the amount of web expansion be digitalized? That is, can the expansion amount be expressed by a mathematical formula? |
Tsuchida: |
It is very difficult to express web expansion amount mathematically due to the presence of so many fluctuation factors, but this basic theoretical formula may be considered. The web expansion amount (W) varies with the inclination angle of a FE roll (inclination angle of each end member)( ), a web's traveling distance per unit time (L), a web's slip coefficient (Ks), and a web's flexibility coefficient (Km), in addition to ambient temperature, humidity, line tension, web composition and the like. Now, when digitalizing in simplest form, the web expansion amount (W) may be expressed by the following formula:
|
|
This means that the web expansion amount is related not only to roll inclination angle, but also with line speed, web slippage and flexibility, isn't it? Please explain this in more detail next time. |